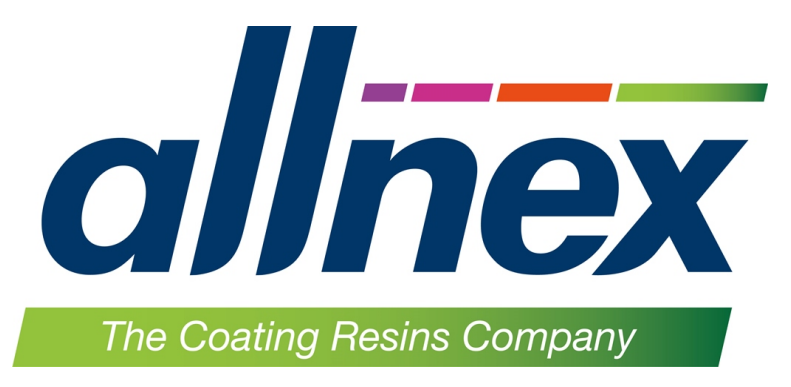
System do budowy form Allnex
Nienasycone żywice poliestrowe oraz epoksydowe stosowane do budowy form
O jakości wyrobów opuszczających fabryki produkujące elementy z tworzyw sztucznych zbrojonych włóknem szklanym w dużej mierze decyduje jakość użytej formy.
Oferta materiałów narzędziowych CHEM4POL-u obejmuje produkty dwóch producentów: Allnex Viapal to żywice i żelkoty poliestrowe.
Produkty Allnex dedykowane są do konstrukcji klasycznych form o strukturze monolitycznej, w których zbrojeniem jest mata z włókna szklanego, ewentualnie w formach zastosowany jest materiał przekładkowy – pianka lub balsa.
System narzędziowy Allnex Viapal
Klasyczne żywice i żelkoty narzędziowe, są ze względu na łatwość przetwarzania podstawowymi materiałami do budowy form. Narzędzia zbudowane z żywic poliestrowych stosuje się z następujących procesach:
- laminowanie kontaktowe,
- odlewnictwo,
- wtrysk żywicy,
- infuzja próżniowa,
- tłoczenie.
Konstrukcja formy z wykorzystaniem żelkotu narzędziowego Allnex Viapal
Konstrukcja formy jak już napisałem we wstępie, wymaga wielkiej dokładności i powinna być wykonywana przez wykwalifikowany personel. Cały dodatkowy czas włożony w proces produkcyjny na tym etapie, powinien zagwarantować wyższą jakość później formowanych elementów.
- Rozdzielacz – na wstępnie przygotowany model (przeszlifowany i wypolerowany na wysoki połysk) należy nałożyć trzy warstwy wosku rozdzielającego KONECA STW. Następnie model należy pokryć jedną warstwą rozdzielacza PVA. Rozdzielacz ten nakłada się przy pomocy pędzla lub miękkiej gąbki. Grubość powłoki powinna wynieść ok 100 µm (100 g/m2). Na tym etapie należy szczególnie uważać, by nie zabrudzić przygotowywanej powierzchni. Proces wysychania powinien trwać ok. 30 minut w temperaturze 20 o
- Żelkot narzędziowy – powinien charakteryzować się ekstremalną odpornością na działanie styrenu (rys. 1), szczególnie w wysokich temperaturach, dużą wartością wydłużenia przy zerwaniu oraz bardzo wysoką odpornością na uderzenia. Warunki te są bardzo dobrze spełniane przez żelkoty Viapal 935 BE i 936 BE.
Żelkot Viapal 935 BE jest dedykowany do aplikacji ręcznej zaś Viapal 936 BE do natryskiwania. Występuje w wersji bezbarwnej oraz w modyfikacji barwionej pastami pigmentowymi z oferty Allnex. Końcowa grubość mokrej powłoki żelkotowej powinna wynieść 800-1000 µm.
Formulacja produkcyjna:
Żelkot zaleca się nakładać w dwóch warstwach. Pierwsza warstwa nakładana jest w warstwie o grubości 0,5 mm. Po utwardzeniu (lepki, ale utwardzony) nakładana jest następna warstwa – 0,3 mm.
Formulacja żelkotu narzędziowego:
100 cz. wag. żelkot narzędziowy Viapal 935 BE lub Viapal 936 BE
4-6 cz. wag. pasta pigmentowa Viapal
2 cz. obj. Utwardzacz MEKP o wysokiej reaktywności
Do budowy większych form lub przy wyższych temperaturach otoczenia zaleca się użycie utwardzaczy o niższej reaktywności.
- Laminat barierowy – żywica barierowa powinna być nałożona po utwardzeniu żelkotu (niezwłocznie po pozytywnym wyniku testu polegającego na przeciągnięciu palcem po powierzchni powłoki). Zadaniem laminatu barierowego jest połącznie niezbrojonej warstwy żelkotu z laminatem konstrukcyjnym zbrojonym włóknem szklanym. Ze względu na ekstremalnie wysoką odporność na działanie styrenu wymagane jest użycie żywicy Viapal VUP 4774 BET/57 zbrojonej matą proszkową o gramaturze 225 g/m2, TEX 10 i proporcji żywica : szło na poziomie 80:20. O późniejszej jakości tej warstwy decyduje w znacznym stopniu jakość jej wykonania. Każdy pęcherz powietrza pozostawiony w strukturze kompozytu obniża trwałość i jakość formy.
Formulacja żywicy barierowej:
100 cz. wag. Viapal VUP 4774 BET/57
2 cz. obj. nadtlenek cykloheksanonu (średnioreaktywny)
Czas żelowania w 20 oC: 50 +/- 5 minut
Użycie nadtlenku cykloheksanonu pozwala uniknąć zjawiska „zafalowania” powłoki żelkotowej oraz skurczu, który może się objawić tuż po odformowaniu .
- Właściwy laminat konstrukcyjny – w zależności od przeznaczenia formy – można go wykonać z użyciem przyspieszonych żywic bez skurczowych lub w klasycznym, bardziej czasochłonnym procesie, pozwalającym uzyskać narzędzie o podwyższonej wytrzymałości – korzystając z oftoftalowych żywic konstrukcyjnych.
Struktura laminatu może być zbudowana tylko i wyłącznie z laminatu zbrojonego włóknem szklanym lub z użyciem materiałów przekładkowych.
- Odformowanie – ze względu na niebezpieczeństwo odkształceń i zaburzenie procesu dotwardzania, nie powinno nastąpić wcześniej niż tydzień od zakończenia budowy narzędzia. Temperatura otoczenia nie powinna być niższa niż 20 o
- Przygotowanie powierzchni formy – wszelkie pozostałości środka rozdzielającego powinny zostać usunięte. W tym celu formę należy zmyć ciepłą wodą z dodatkiem mydła lub detergentu. W zależności od potrzeb – powierzchnia formy może zostać wypolerowana na wysoki połysk. Do procesu szlifowania i polerowania zalecamy pasty polerskie KONECA HCP (do wstępnej obróbki) i KONECA LCP (do wyrównywania pozostałych nierówności i nabłyszczania wyrobu). Nowo przygotowana forma, jeszcze przed użyciem powinna zostać pokryta rozdzielaczem na bazie PVA.
Skontaktuj się z nami
Masz pytania? Zapraszamy do kontaktu!
Nasz sztab specjalistów jest do Twojej dyspozycji!